
精密的表面处理

对具有严格公差的精密部件进行卓越的表面处理,提高机械性能、使用寿命和耐腐蚀性。

市场上越来越苛刻的质量标准极大地提高了精密表面处理工艺的重要性。 原因很清楚,因为毫无疑问,表面精加工处理不仅能改善金属零件的外观美感,还能改善其机械和物理特性、耐腐蚀性和使用寿命等。 当部件被用于与重大压力或攻击性制剂有关的环境中,或当产品有特殊的处理需要时,这些处理通常是必要的。
一个事实是,今天的制造商要求金属零件生产商提供极其一致和可靠的工艺。 除此之外,根据目前的市场需求,零件的长期耐久性必须是可重复的,性能必须得到保证,以稳定各行各业的精密部件的质量。
一些需要精密表面处理工艺的部件是工具、传动部件、涡轮机和具有功能应用的装配部件。
由于DLyte的存在,这类工件有可能获得高标准的表面平整度、光滑度和几何精度。 由于它的精度、低材料去除率和边缘保护,它特别适用于需要出色的表面精加工的零件,完全保持边缘和严格的公差,否则无法自动处理。 反过来,干式电抛光可以实现自动化流程 ,保证各批次的结果一致。


精细加工成功案例
常见应用





抚平

光滑的表面处理可以减少摩擦损失,提高轴承比率,优化磨损,最大限度地减少能源消耗和噪音。

用DLyte磨平金属表面
工业零件通常需要光滑的表面以符合其功能。 金属工件需要进行光滑处理,不仅是在预处理过程中造成不平整的情况下,还需要去除磨痕或划痕,或用于平整铸件和锻件的表面。 对于运动部件,如变速箱、涡轮机、阀门、轴承、成形工具或主轴,光滑的表面可以减少摩擦损失。
DLyte表面抛光有选择地光滑金属表面到所需的表面质量的工件由各种各样的材料,如,钢,不锈钢,铝或黄铜。平滑操作提高了零件的美观性和质量感知,优化了磨损,最大限度地减少了能耗和噪音。
干式电抛光工艺在表面上达到均匀的结果,消除了微划痕和铣削线。 该系统在微观和宏观层面都有效运行。它增强了负表面偏度(rsk),增加了表面轴承接触面积——因此,允许均匀的润滑油膜分布–提高轴承比,减少金属零件之间的摩擦和噪声。
此外,干式电抛光尊重公差并保留工件的初始形状,甚至是切割边缘,避免产生磨削纹理图案。 它提供了高的粗糙度降低率和抗腐蚀保护。


常见应用




镜面加工

镜面处理是一种高度抛光的处理,其特点是金属表面明亮、闪亮、反光。 去除任何微观划痕和铣削线。

用DLyte进行镜面加工
镜面抛光是一种高度抛光的表面,其特点是金属表面明亮、闪亮、反光。 它可以在建筑、运输、消费品等美学部件或针对时尚和奢侈品行业的金属件中找到,也可以在为食品、制药和医疗应用生产的金属件中找到。 高质量的镜面效果不仅在视觉上吸引人,而且通过抛光工艺逐步去除表面划痕,减少了金属上的压痕或沟槽,这些压痕或沟槽可能含有污染物,如灰尘或细菌。 这些表面易于清洁,更耐腐蚀,并能发现设计缺陷。
除了在美学上有明显的改进外,镜面处理的作品比粗糙的表面更不容易受到污染。 光滑的表面是通过在机械应用中使用不同的研磨剂来逐步去除金属上的划痕和瑕疵而实现的。 例如,在更多的技术术语中,镜面加工的钢的Ra指数在0.15(6微英寸)和0.3(12微英寸)- Ra之间。 即:关于粗糙度平均值,它衡量的是金属表面的微观波峰和波谷,数字越小,波峰和波谷就越少或越小,这意味着抛光后的金属表面看起来更光滑,更亮丽。
干式电抛光工艺在整个表面实现了均匀的结果,并消除了微观划痕和铣削线。 该系统在微观和宏观层面上高效工作。 它们还增强了负表面偏斜度(rsk),增加了表面轴承接触面积–因此,允许均匀的润滑油膜分布–改善了轴承比率并减少了金属部件之间的摩擦。 此外,干式电抛光尊重公差并保留工件的初始形状,甚至是切割边缘,避免产生磨削纹理图案。 它提供同类最佳的表面粗糙度(Ra低于0.01微米)和防腐蚀保护。






镜面加工成功案例
常见应用


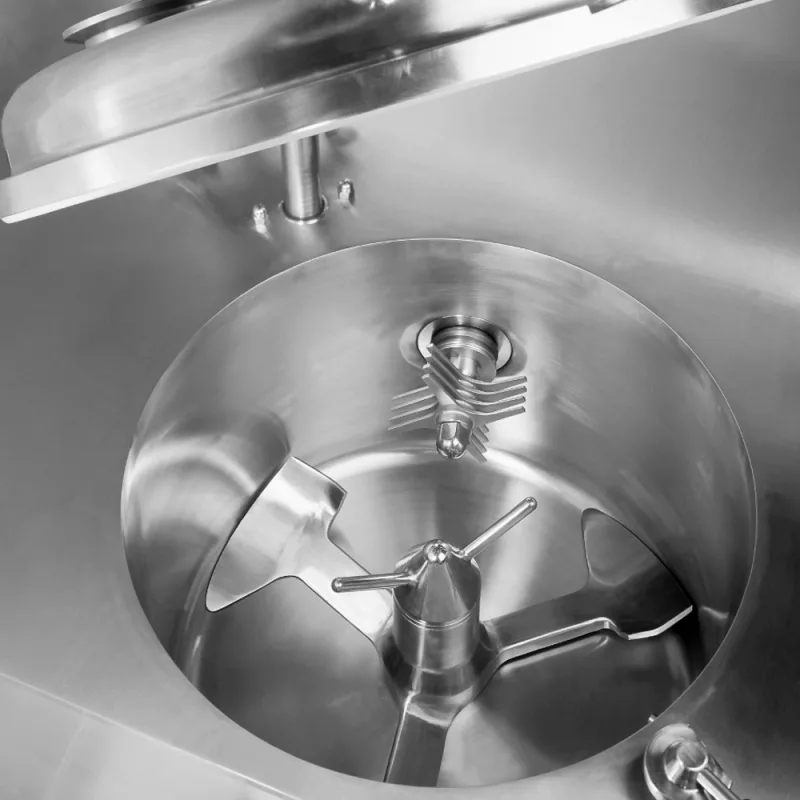












去毛刺

从锋利或脆弱的零件上去除毛刺,这些零件不适合采用传统的精加工技术,而不会使边缘变圆或损坏零件。

用DLyte去毛刺
去毛刺是一种材料改性工艺, 通过去除以前加工过程中留下的 毛刺来提高产品的最终质量。 DLyte是一种有效的自动化工艺,可以从复杂或脆弱的金属部件上去除小毛刺,这些部件不适合采用传统的翻滚或振动精加工技术。
干式电抛光技术改善了目前去毛刺技术的效果。 它克服了液体电抛光和研磨抛光的障碍,使用固体颗粒通过离子交换去除材料。 由于它是一种非磨蚀性的处理,因此不会使边缘变圆。 该工艺能够去除毛刺、表面的污染,并在一个过程中提高耐腐蚀性和表面质量。
毛刺可以被定义为工具或机器的作用在物体上留下的尖锐缺陷、粗糙边缘或脊线。 它们是对光滑加工表面的功能或外观有负面影响的杂质。 毛刺是由弯曲、切割、刺穿、剪切和压缩材料产生的,大多见于韧性和软性材料。 当弯曲或剪切力被施加到失效时,金属和合金可能会因塑性变形而变硬。 沿着边缘的区域变得弯曲、挤压或拉长。 这些挤压和伸长出现在切削刃上,主要是在金属工具的入口、侧面和出口。
毛刺可能影响金属制品的质量,使其表面不光滑。 更重要的是,金属表面存在的毛刺会造成一些问题。 事实上,这些缺陷妨碍了工件的配合和装配,增加了腐蚀、疲劳和裂纹的风险,并可能陷于污染;对工件的美学效果有不好的影响,并可能造成操作者和最终用户的安全隐患。 这就是为什么去毛刺在加工食品、制药、医疗或航空航天领域的高要求零件时是必不可少的。




技术优势
干式电解抛光技术是一种新颖的电化学工艺,特别推荐用于去除零件上的小毛刺。 由于干式电抛光不是一个机械过程,金属的硬度对毛刺的去除没有影响。 此外,它还适用于退火或硬化的金属部件。 因此,干式电抛光可以在所有的制造过程之后进行最后的去毛刺。
另一方面,干式电抛光不是一个扭曲的过程。 现在制造的金属件的主要部分有关键的微观处理,或由更脆弱、更轻的材料制成。 当它发生时,大规模的精加工技术,如翻滚或振动精加工,会产生翘曲或变形,并会出现缺口或划伤精细精加工。 干式电抛光件不会受到抛光介质的应力影响,也不会相互翻滚。
经济和环境效益





四舍五入

切削刃的几何形状决定了刀具所承受的热机械应力。 通过有控制的边缘准备来增加其寿命。

用DLyte将切割边缘磨圆
圆滑的切削刃,也被称为切削刃半径或刃口准备,是关于加工金属的切削刃的微观设计和几何形状的关键参数之一。 切削刃的几何形状决定了刀具所承受的热机械应力,刃口准备可以提高刀具寿命、切削性能和加工表面质量。
一些研究表明,将切削刃磨圆到一个特定的微米值,可以增加50%以上的刀具寿命,因为硬质材料很脆,其锋利的边缘容易剥落和快速磨损。 要认识到因未准备好的切削刃而产生的问题,会出现过早的故障或加工件表面质量下降。 立磨会有崩裂、材料粘连、涂层剥落和堆积边缘的痕迹。
DLyte是一种有效的自动化工艺,可根据制造商的要求将立铣刀、硬质合金刀片和硬质合金铰刀 的切削刃磨圆至特定半径,并同时改善刃口的表面质量,从而使切屑流动更快,增加切屑量。 干式电抛光技术改善了目前圆角技术的结果。 它克服了磨料抛光的障碍,使用固体颗粒通过离子交换去除材料,即使是非常坚硬的材料,如硬质合金。 由于它是一种非磨蚀性的处理方法,它在刃口光滑度和刃口半径之间保持了良好的平衡,增加了刀具的使用寿命,从而减少了刀具磨损。
DLyte能够在涂层后对切削工具进行加工,从而使工具表面光滑,提高排屑率、工具寿命和加工表面的质量。

成功案例
常见应用




抗腐蚀能力

提高抗腐蚀能力,去除嵌入的游离铁、污染物和热染色剂或氧化鳞,并在一个步骤中减少表面粗糙度。

干式电抛光以提高耐腐蚀性
耐腐蚀性是描述由于环境中的化学反应而导致的金属内在属性恶化的参数。 这个术语不仅由金属和合金的化学成分定义,还由许多其他因素定义,如紧固件设计、表面质量、应力集中和裂纹。 环境因素,如氯离子浓度、腐蚀环境的化学成分、温度、pH值、压力和氧化剂也是决定抗性的重要因素。
干式电抛光是一种电化学精加工,从金属件上去除一层薄薄的材料,如钛、钴铬、铜、铝或不锈钢等等。 这项技术是增强金属零件的抗腐蚀性和改善其表面质量的首选方法。 该技术使金属部件的耐腐蚀性比钝化高出30倍。 因此,已经取代了钝化,成为改善耐腐蚀性的最受欢迎的方法。 此外,能够去除嵌入的游离铁、污染物和热着色或氧化鳞,并在一次操作中降低表面的粗糙度。
钝化是一种化学金属表面处理工艺,以提高不锈钢部件的耐腐蚀性。 对于这种金属,钝化过程使用柠檬酸或硝酸来消除表面的游离铁等铁类污染物。 化学处理导致了一个保护性的氧化层,不太可能与空气发生化学反应并导致腐蚀。 钝化的工作原理是将待处理的金属部分浸入酸浴中。 这种物质可以溶解表面的任何游离铁或其他污染物,从而清洁金属,并且可以使铬重新氧化。


为什么干式电解抛光比钝化处理更能防止腐蚀?
如前所述,电抛光和钝化都是可以提高耐腐蚀性的方法。 不管怎么说,相似之处到此为止。 这些是电抛光工艺相对于钝化的一些主要优点:
- 干式电解抛光比钝化处理更有效地提高了耐腐蚀性能30倍
- 干式电解抛光可同时进行增亮和抛光处理
- 它对所有等级的不锈钢都有效
- 它适用于 去毛刺
- 它同时还能使金属部件钝化,从而提高表面质量
- 干式电解抛光适用于不能被钝化的金属合金,例如钛或镍合金。
- 它可以改善微细加工和耐腐蚀性
- 它可以去除热染色剂和氧化层
- 与钝化不同,干式电解抛光不需要任何预清洁操作
为什么干式电抛光比液体电抛光更能防止腐蚀和改善表面?
一件设备的耐腐蚀性不仅取决于选择最合适的合金,而且还取决于对材料的正确处理。许多应用需要在磨光、去毛刺或抛光后进行表面处理,以完成耐腐蚀性要求。
干式电解抛光是唯一能够大幅度去除粗糙度并在一个步骤中提高金属件的耐腐蚀性的技术,同时减少制造过程中所需要的工序数量。 相比之下,传统的电抛光只能在初始粗糙度的基础上减少50%的粗糙度。

经济和环境效益





抗腐蚀成功案例
常见应用

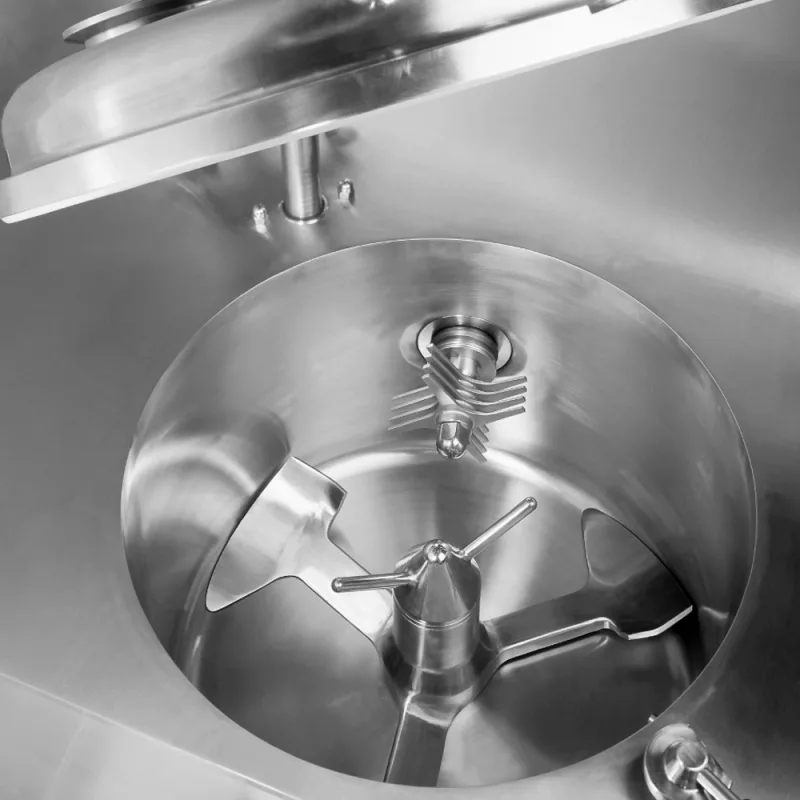


AM 后期处理

在不损失公差的情况下,实现添加剂部件的表面精加工自动化。 在减少粗糙度和保留几何形状之间取得最佳平衡。

增材制造零件的后处理
增材制造(AM)是一种生产过程,材料以受控方式逐层沉积在需要的地方。 这项技术允许生产具有新的几何形状和形状的零件,这在以前是不可能的。
与传统的制造技术相比,它还减少了中间过程,如模具生产,使其有可能更快、更经济地获得短系列的零件,以及原型设计和定制产品。
后处理的AM零件约占总成本的30%,占这些零件生产总时间的50%。 与传统制造业相比,缺乏自动化的表面处理程序是发展AM产业的一大障碍。
DLyte对金属增材制造部件进行自动化的有效表面处理,从而极大地提高了它们的性能和寿命。 基于干式电抛光的专利技术可以在不改变几何形状的情况下大幅度地改善表面。
DLyte表面处理有选择地改善金属表面,使工件达到理想的表面质量。 材料范围还包括非常难以侵蚀的材料,如镍合金、钛合金和硬质合金。
DLyte的DryLyte被认为是金属增材制造零件的表面精加工技术,在降低粗糙度和保留几何形状之间具有最佳的平衡。它还能实现最低的表面粗糙度,比市场上次好的替代品至少低2倍。它还适用于精巧和脆弱的工件,而不会对其造成伤害,因为该工艺不使用研磨剂,也不使用强大的机械力。
与磨料相比,这些方法不会对表面造成压力,不会在光滑的表面上造成划痕,也不会像磨料那样在金属表面产生夹杂物。 这些工艺与磨料相比的另一个优势是,它们不会产生灰尘残余或噪音。
DryLyte技术在2018年和2022年被授予TCT增材制造后处理卓越奖。
在AM金属零件中进行适当精加工的好处
AM部件需要准确地完成。 有一些原因可以证明表面处理的重要性。
表面处理使得有选择地在各种材料制成的工件上达到所需的表面质量成为可能,如钢、不锈钢、铝或黄铜。 因为这个过程相当于去毛刺,毛刺从工件上不可触及或难以触及的位置被去除,同时其边缘也被去毛刺和磨圆。
表面处理的质量将基本上取决于机器的类型和设置,以及零件的材料。
使用磨料物质进行这一过程是很常见的,其使用可能会产生比磨料较少的表面更粗糙。 尽管如此,也可以通过选择磨料体的特定几何形状来控制粗糙度模式,也可以通过使用侵蚀性较低的工艺,如DLyte的电解抛光解决方案。
如果你对AM金属零件的表面处理有任何疑问或怀疑,不要犹豫,请联系我们的专家团队。

技术优势
经济和环境效益





常见应用






内部通道抛光

以成本效益高、可靠和质量好的方式提高内槽和带盲孔的复杂金属零件的表面质量。

用DLyte对内部通道进行抛光
在过去几年中,对内表面、内部通道和带有盲孔的复杂部件的表面质量要求越来越高,特别是在注塑成型、航空航天、汽车、医疗、食品和制药、半导体以及气体和液体流动应用方面。 此外,新的制造方法,如增材制造,具有创造复杂零件的能力,但表面质量差,增加了对内部区域表面处理的需求。
大多数需要内部抛光的应用要求低粗糙度和无毛刺,以提高流速并减少因低摩擦而产生的湍流,一个惰性的、光滑的表面,只有很少的位置可以捕获杂质并避免生物膜的形成,以及在部件暴露于氧化剂时的抗腐蚀能力。 目前的表面处理技术,如磨料机械、化学和手工处理,都不能有效地处理这些情况,从而达到次优的效果。
DLyte使用新颖的干式悬浮电抛光工艺对金属零件进行成本效益高、可靠、质量上乘和惰性的内表面处理。 它在一个单一的过程中包含了机械和电化学过程的好处,因为DLyte改善了处理内部通道的替代程序的结果,如磨料流加工和液体电抛光。
该解决方案能够提供平均粗糙度Ra低于0.3微米的表面,并且相对于原始和液体电抛光表面而言,提高了耐腐蚀性,从而实现了超高纯和高纯部件的目标。 最小直径为4毫米的直槽或直角和钝角可以进行内部抛光。
通过订阅我们的通讯,了解金属表面处理领域的最新创新。